Metal Stamping: Advanced Techniques for Achieving Accuracy and Efficiency
Advanced Techniques in Steel Stamping for Accuracy Production
As sectors constantly require better tolerances and complex layouts in their metal elements, the pursuit for advanced methods in steel stamping has intensified. From the use of innovative multi-stage stamping procedures to the assimilation of cutting-edge automation innovations, the landscape of steel marking is going through an extensive transformation.
Advanced Multi-Stage Stamping Processes
Discussing the complexities of innovative multi-stage marking processes discloses the sophisticated methods employed in modern production practices. Metal Stamping. Multi-stage marking is a complicated procedure that includes multiple actions to change a flat sheet of steel into a last stamped product. The usage of modern dies, where different operations are done at each phase of the stamping process, allows for high precision and efficiency in the manufacturing of elaborate metal parts
Throughout the first phases of multi-stage marking, the level steel sheet is fed into the stamping press, where a series of dies are used to cut and shape the product. Subsequent phases entail added forming, bending, and punching procedures to more refine the component. Each phase is very carefully designed to construct upon the previous one, leading to the creation of complex geometries with tight resistances.
Advanced multi-stage stamping procedures call for a high level of proficiency and accuracy to make certain the quality and consistency of the stamped parts. By making use of advanced equipment and tooling, producers can generate a broad array of metal elements with efficiency and precision.
Accuracy Tooling Innovations
Precision tooling developments have revolutionized the steel marking industry, enhancing effectiveness and quality in making processes. These advancements have actually substantially impacted the means metal parts are produced, leading to greater precision and uniformity in the end products. One essential technology is the growth of computer system mathematical control (CNC) innovation in tooling layout and construction. CNC systems enable complex styles to be converted directly right into tooling, ensuring precision and repeatability in the marking process.
Moreover, the assimilation of sensing units and real-time monitoring capabilities in precision tooling has enabled makers to detect and address issues quickly, reducing downtime and minimizing scrap rates. By integrating wise modern technology into tooling, operators can optimize parameters such as stress, speed, and alignment during the marking procedure, leading to improved item high quality and enhanced productivity.
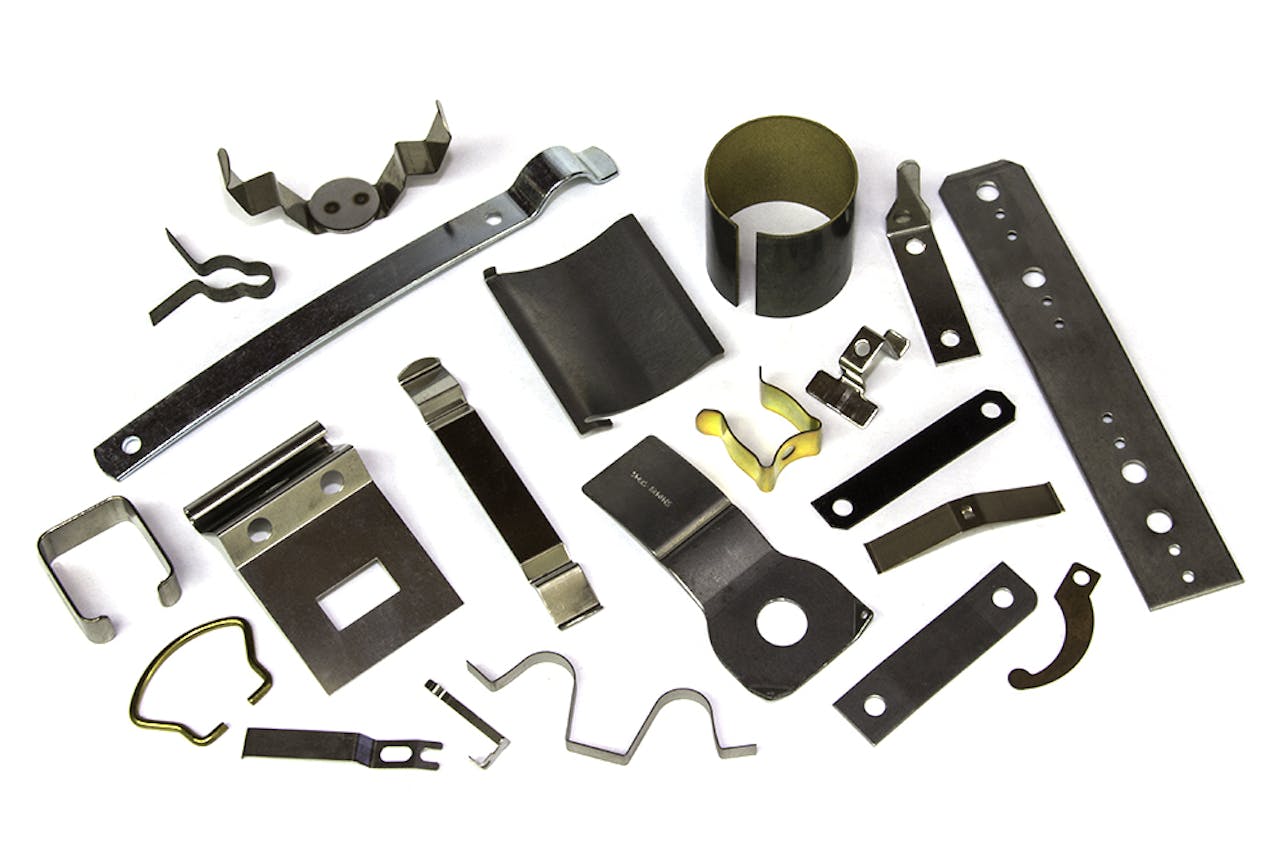
Automation in Metal Stamping
The evolution of accuracy tooling advancements in the steel marking industry has actually led the way for substantial improvements in automation, transforming the manufacturing landscape in the direction of enhanced performance and productivity. Metal Stamping. Automation in steel stamping sites involves making use of innovative machinery and robotics to carry out various jobs generally executed by human drivers. This shift in the direction of automation supplies countless benefits, including enhanced precision, quicker production cycles, and decreased labor costs
One secret element of automation in metal stamping is the execution of computer system numerical control (CNC) systems, which enable exact control over the stamping procedure. CNC technology permits the production of complex and complex steel get rid of regular quality. Additionally, automated systems can be set to run continually, causing higher outcome prices and much shorter lead times.
Additionally, automation enhances workplace security by minimizing hand-operated handling of heavy products and reducing the threat of crashes (Metal Stamping). As making sectors remain to embrace automation, the future of metal marking holds fantastic pledge for even higher performance and advancement
High-Speed Stamping Methods

Among the main advantages of high-speed stamping methods is the capacity to produce a big quantity of parts in a much shorter quantity of time contrasted to typical marking methods. This enhanced productivity not only allows makers to fulfill tight manufacturing target dates however additionally makes it possible for expense financial savings via economic climates of range. Additionally, high-speed marking can help in reducing material waste by optimizing the product usage throughout the stamping process.
Additionally, high-speed stamping techniques typically integrate cutting-edge features such as fast die change systems and real-time surveillance abilities, click here for more further boosting the general effectiveness and flexibility of the steel stamping process. As innovation proceeds to development, high-speed marking is anticipated to play a critical duty in driving the future of precision production.
Top Quality Control in Stamping Procedures
Effective quality assurance steps are necessary for making certain the dependability and uniformity of metal stamping procedures. Quality assurance in stamping procedures involves a collection of systematic procedures targeted at discovering and stopping flaws in the produced parts. One critical facet of high quality control in metal stamping is making use of sophisticated examination techniques such as optical evaluation systems and coordinate measuring this hyperlink makers (CMMs) to validate the measurements and resistances of stamped components.
In addition, quality assurance procedures in marking procedures commonly include the implementation of analytical process control (copyright) techniques to monitor the manufacturing process in real-time and ensure that it remains within acceptable restrictions. By evaluating data and identifying fads, suppliers can proactively resolve any type of inconsistencies from the preferred top quality criteria.
Furthermore, top quality control in metal stamping operations also entails thorough product screening to ensure that the raw materials used satisfy the needed requirements for the marking procedure. This may include conducting material firmness tests, tensile stamina examinations, and dimensional examinations to assure the quality and integrity of the stamped components. In general, executing robust high quality control procedures is critical for attaining high-quality stamped components consistently.
Conclusion
Finally, progressed strategies in steel marking play a critical duty in accuracy manufacturing processes. Through multi-stage stamping procedures, cutting-edge tooling remedies, automation, high-speed strategies, and extensive quality assurance steps, producers can achieve higher degrees of accuracy and performance in their procedures. These improvements in metal stamping technology have actually allowed companies to produce intricate components with tight resistances, inevitably causing improved item top quality and client fulfillment in the manufacturing sector.